HOW THE DESIGN OF THERMAL LANCES PROVIDES VARYING PRECISION DEGREES AND CONTRIBUTES TO THE CARE COMPONENTS INVOLVED IN TAPPING OF OPERATIONS.
Within pyrometallurgy, in smelters, thermal lances have been commonly used to open furnace passages. Despite their routine use and seeming to be a simple and insignificant element, the lances have undergone a process of innovation in design that has resulted in lances capable of maximizing the generation of thermal energy in the same diameter and distributing this energy to make precision drilling and cutting.
In general, the operation of a thermal lance is based on the combustion of the steel that it is made, so its distribution in the cross section determines the direction of the energy projection that each model of thermal lances will have.

Figure 1. Profiles of the Trefimet thermal lances.
The different configurations allow to maximize the amount of steel in the cross section, which generates a better use of oxygen and concentrates a greater amount of energy in a smaller area. Another important point to highlight from these designs, is how it is distributed from the central axis of the cast.
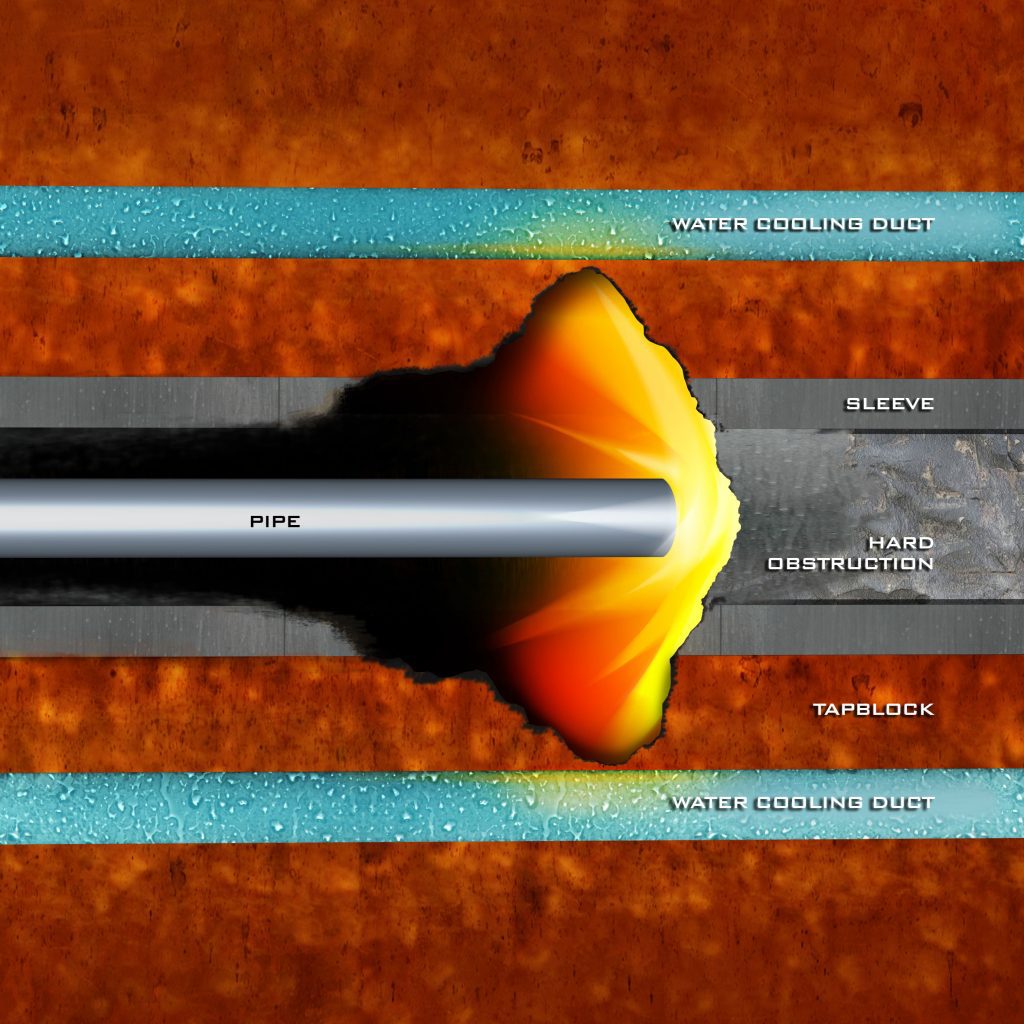
In the case of an common tube (known as a "pipe"), all the steel is found in the peripheral area of the lance, so the energy projection takes a radial direction, while in the models with more steel in the central part of the lance, the projection direction is axial. This point is extremely important, since in narrow passages or precision works such as tuyeres cleaning, there are components that you do not want to damage that are very close to the work point, so it is very important to attack only what is needed to melt.
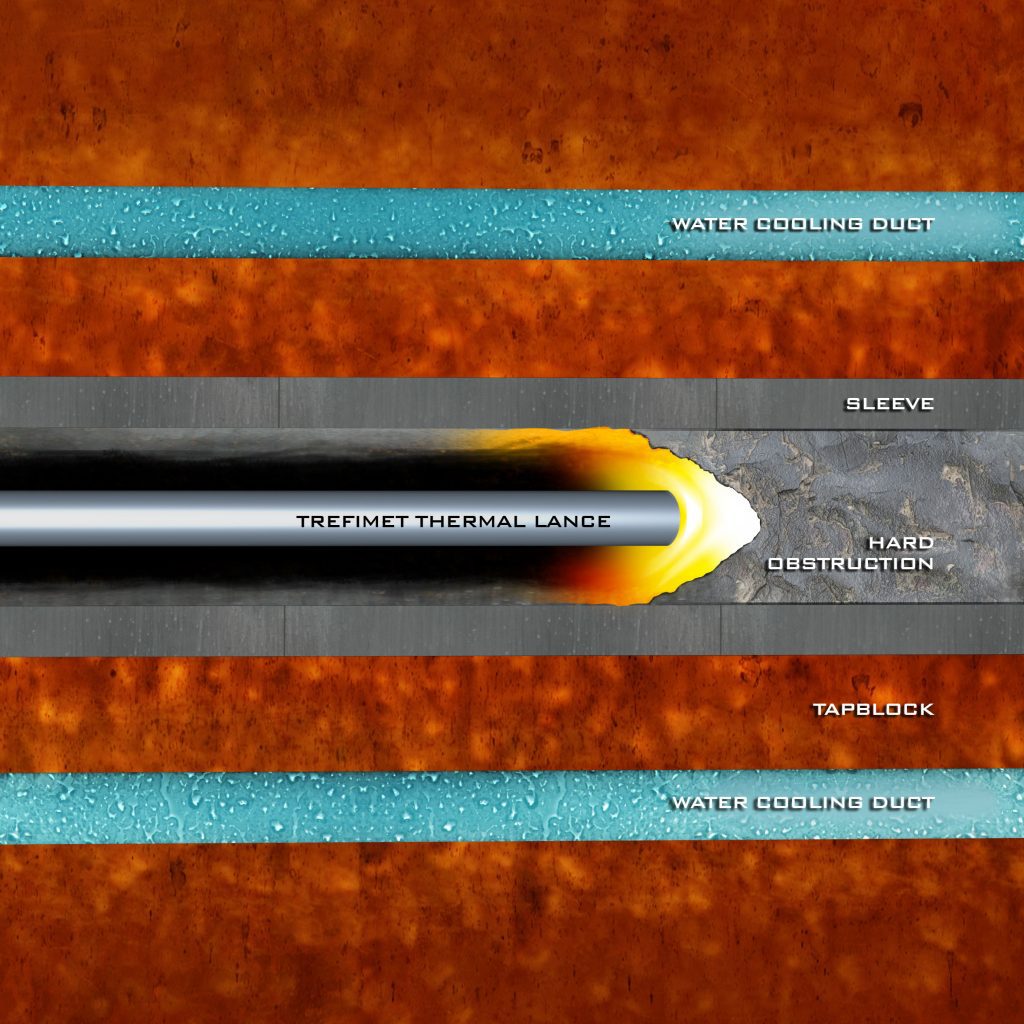
Besides from projecting the energy in an axial direction, by having a greater quantity of steel in the same area, these casts can pass through the same material much faster than the pipe, generating smaller perforation diameters and achieving the same task in a shorter time.
All these points of improvement in the designs of the thermal lances, also provides performances and reduced operating times, notably improves the lifespan of the taphole face plates and extend the maintenance periods, generating an improvement in productivity.
There has been an increase in the useful life of some tapholes of up to 50% and tuyeres cleaning operations where it is possible to remove the material inside these without damaging the structure.