How does the design of thermal lances deliver varying degrees of precision and care for the components involved in the bleeding operation?
Within pyrometallurgy, in smelters, thermal lances have been commonly used to open furnace passages. Despite their routine use and seeming simple and insignificant, thermal lances have undergone a process of design innovation that has resulted in lances capable of maximising thermal energy generation in the same diameter and in distributing this energy for precision piercing and cutting.
In general, the operation of a thermal lance is based on the combustion of the steel of which it is composed, so the distribution of the steel in the cross section determines the direction of the energy projection that each model of thermal lance will have.
The common lances consist of an outer tube filled with wires or a simple tube usually called a "pipe".
Trefimet is dedicated to optimising its model designs for different types of operations, with different components inside and different geometric shapes in contact with each other.

The different configurations maximise the amount of steel in the cross-section, which generates greater oxygen utilisation and concentrates a greater amount of energy in a smaller area. Another important point to note about these designs, apart from the concentration of steel in the cross-sectional area, is how it is distributed from the central axis of the lance.
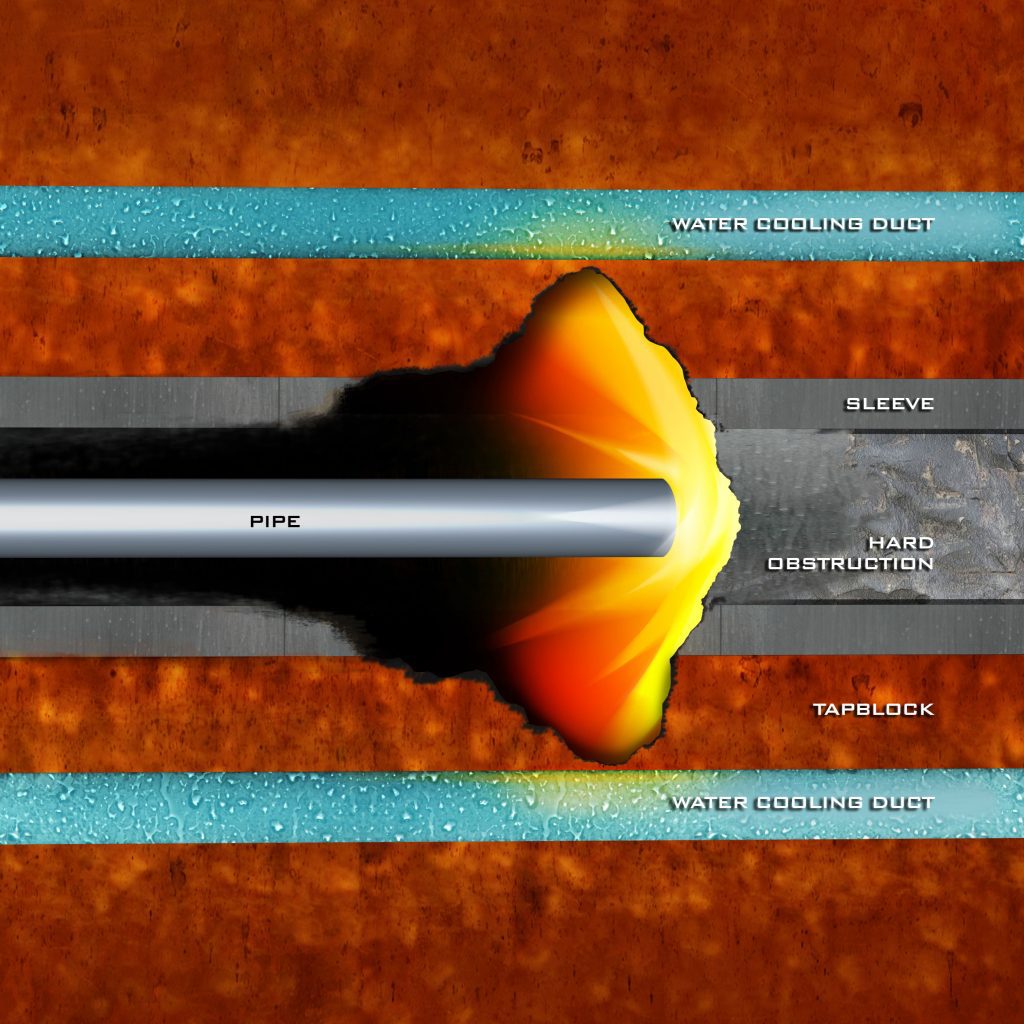
In the case of an ordinary pipe, all the steel is in the peripheral area of the lance, so the energy projection takes a radial direction, whereas in models with more steel in the central part of the lance, the direction of the projection is axial. This point is of utmost importance, since in narrow passages or precision work such as nozzle cleaning, there are components that you do not want to damage and which are very close to the working point, so it is very important to attack only what you want to melt.
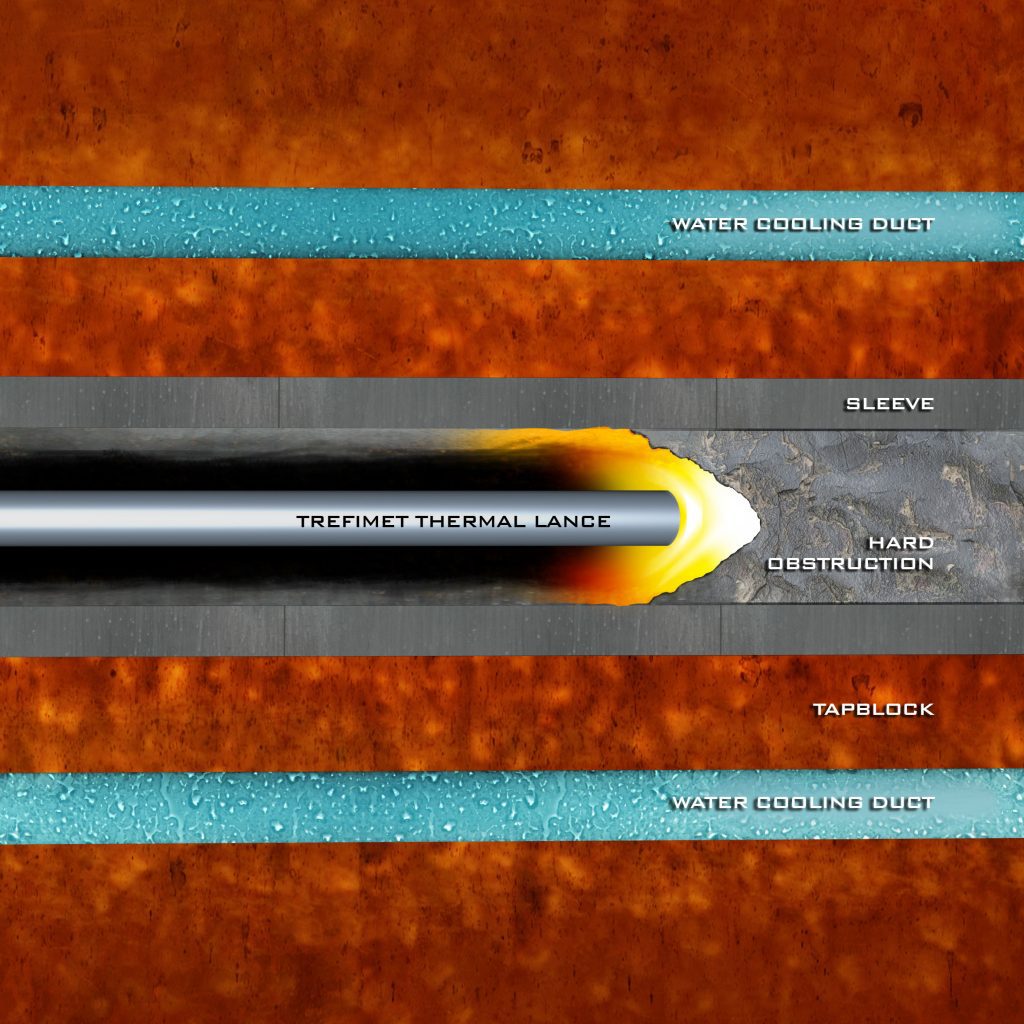
In addition to projecting energy in an axial direction, by having more steel in the same area, these lances pass through the same material faster, generating smaller bore diameters and achieving the opening target in a shorter time.
All these improvements in the design of the thermal lances, apart from translating into better performance and reduced operating times, significantly improve the useful life of the passage plates and extend their maintenance periods, generating an improvement in productivity.
An increase in the useful life of some passages of up to 50% has been recorded and nozzle cleaning operations have been carried out, where it is possible to remove the material inside the nozzles without damaging the structure.